Tagore tried to save Bengal’s Shellac Doll Art
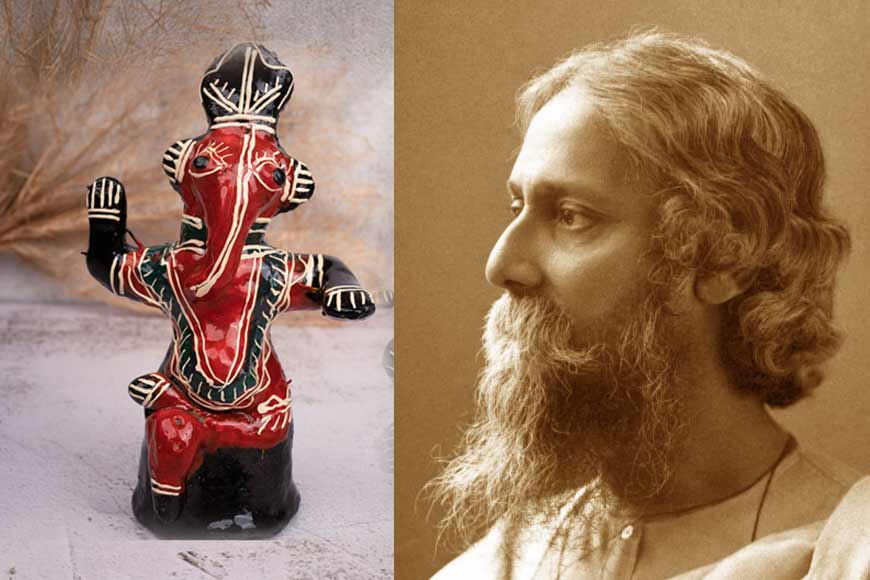
Whenever we think of dolls made of shellac, the first thing that comes to mind is the shellac dolls of Birbhum. The Nuri community of Ilambazar was once renowned for producing attractive shellac dolls, as it was readily available in this region. The artisans used to collect lac in small communities left over after mass production, extracted from the sticky dye of the insect’s body that they mixed with clay and various colours. This mixture was used as a coating for producing attractive dolls. With the decline of the shellac industry in Birbhum owing to a shortage of raw materials, the future of such doll production is somewhat in the dark. Yet they are made.
The progressive decline of this art of toy making did not escape the notice of even Rabindranath Tagore, who had devoted his efforts to restoring this dwindling industry. At his invitation, an artist of the Nuri community came down to Sriniketan and started holding training sessions for interested art students. It led to the revival of the production of various types of shellac dolls and fruits in conformity with age-old procedures. A distinctive characteristic of these dolls is their shapes.
Some displayed a mother with a child in her arms, a woman tying up her companion’s hair, a man husking paddy, a mahout riding an elephant, a horse rider, and an endless variety of fruits such as mango, custard apple, lychee, bitter gourd and several types of lemons. But with the cultivation of lac gradually coming to a halt and a lack of enthusiasm among artisans, this old traditional industry is on the brink of existence.
While the industry almost wiped out from Birbhum, another type of doll with a layer of shellac applied to them came into existence in Bankura and Medinipur districts. The center of production of these dolls was Shankharibazar of Bishnupur, from where shellac-painted dolls were carried for sale to village fairs during religious festivals.
The production of shellac-painted dolls is quite common in Medinipur and the artisans are not just selling them in the local markets. They sell them in large numbers in various fairs of Orissa, like in Baripada where there is a huge demand for these dolls. The demand particularly increases during the Rathayatra festival. During this time, there occurs hectic activities among the women of these families, shell workers of Panchrol under Egra police station and Kharui Bazaar under Patashpur Police Station. Both these villages are close to the Orissa border.
Around 3-4 families are still in the doll business. The main attraction of these dolls lies in the large assortment of colours, which are rendered exceptionally bright through the expert mixing of shellac and paint. The production process of these dolls is also quite amazing. First, a figure is constructed out of a lump of clay with fingers, without using molds. As a result, the dolls bring out a spirit of simplicity. The artisans also produce dolls resembling animals like elephants, horses, deer, and oxen, idols of various gods and goddesses such as Balaram, Subhadra, Narugopala, Ganesh, Manasha, kings and queens, and horse riders. All these dolls are usually 5-15 cm in height.
Soil collected from white ant hills in and around the villages is soaked in water and preserved in earthen pots or basins. The advantage of this soil gathered is that it does not contain gravel and also has an adhesive property. The soil is still kneaded with hands to free it from small particles of gravel or brick. This procedure is locally called chanchi. Once the lump is dried to an optimum extent, the artisan starts using all ten fingers of his hands to commence his craft. The finished doll is first baked in a domestic oven and then painted in selected colours. For the latter operation, sticks of painted shellac looking like pencils are prepared first. Screened shellac of necessary quantity is mixed with paint powder of desired colours, and the mixture is heated on a fire to produce these sticks. They look like long wood pencils and are normally of four colours --- red, black, yellow, green.
In the next stage, the dolls are stacked in small earthen vessels before they are heated up in a charcoal fire. Usually, an earthen pot is cut off in a crosswise direction, and its upper part is tilted to serve as a receptacle for the charcoal fire. Bamboo pipes are used for blowing air through the mouth so that the fire does not extinguish. The moment the doll is heated to the desired extent, it is inserted into a bamboo kamrha where it is held and painted. The artisans generally prefer to paint the front faces of the dolls in red or green and the rear faces in black. Next, thin shellac threads are taken out from yellow shellac sticks and while they are still hot, these threads are used for providing decorative wearing apparel and ornaments for the dolls. The operation of taking out shellac strings from coloured shellac sticks is termed guna work. Yellow strings are then rolled into balls to serve as eyes and black dots are inserted on them as pupils.
(Data from Folk Arts of West Bengal and the Artist Community by Tarapada Santra)